This article was originally published on AutomationWorld.com on January 13, 2025.
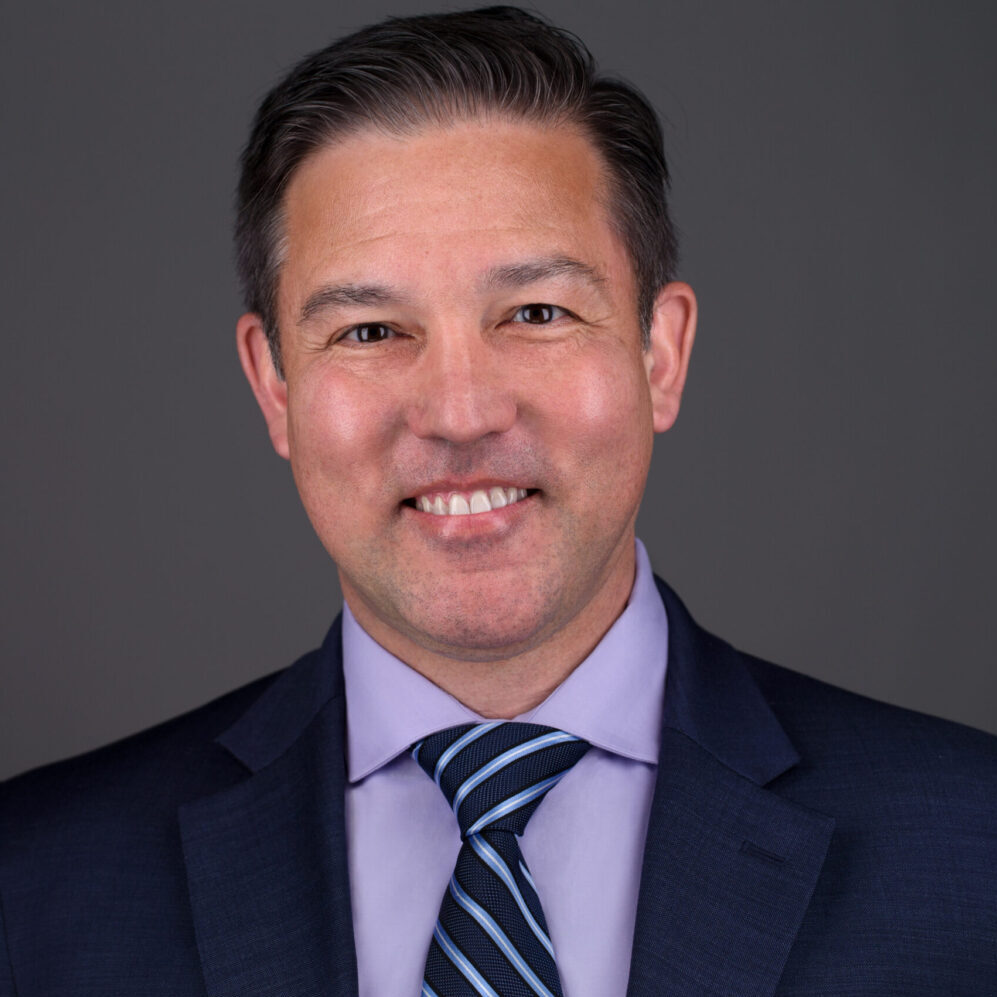
Danny Haskell, President & VP of Sales
By combining real-time monitoring, predictive analytics and proactive maintenance, APM shifts focus from reactive problem-solving to proactive performance optimization.
Manufacturers are under increasing pressure to deliver high-quality products while maximizing production and profitability. However, issues like equipment downtime, inefficient processes and a lack of real-time visibility into asset health can all reduce productivity and increase costs.
This is where asset performance management (APM) comes in.
APM is a data-driven strategy that integrates advanced technologies to monitor, analyze, and optimize the performance and reliability of industrial assets. By combining real-time monitoring, predictive analytics and proactive maintenance planning, APM shifts focus from reactive problem-solving to proactive performance optimization, making it a cornerstone of modern manufacturing.
Real-time insights and standardized data capture
The complexity of asset management has outgrown manual, paper-based tracking systems. Automation engineers need tools to streamline processes, optimize performance and provide real-time visibility into operations. APM addresses these needs by enhancing decision-making with: