Redefine Asset Management with Real-Time Insights and Predictive Analytics
Effective asset performance management is critical to maintaining operational efficiency and minimizing downtime. As production scales and equipment becomes more complex, relying on manual and paper-based systems creates unnecessary risks and inefficiencies. Manufacturers need modern automation solutions that provide real-time insights and streamline asset performance tracking.
Manual and paper-based tracking systems are no longer sufficient to keep up with the complexities of asset management in the manufacturing industry, so if your plant is struggling with:
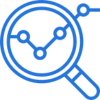
Lack of real-time insights
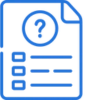
Manual processes leading to errors
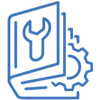
Inefficient paper-based systems
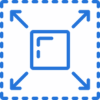
Scalability
issues