CHALLENGE
The company had standardized on platforms for plant floor control (Allen Bradley & Siemens PLCs), MES (Rockwell), CMMS (FIIX) and ERP (SAP) systems. As the implementation of these platforms progressed, it became apparent that a gap existed with their existing software platform implementations and their desire to:
- Provide digital Andon dashboards on ~100 smart TVs throughout their 1M SF manufacturing facility. Andon dashboards increase efficiency across the shop floor by providing operators and supervisors real-time access to critical performance indicators:
- Line/Cell Status (Running, Blocked, Starved, Faulted, Over Cycle)
- Alarm/Fault Status
- Operator Quality, Help and Material Calls
- Jobs Per Hour Actual vs. Target
- Cycle Times
- First Pass Yield
- Buffer Inventory Counts
- OEE (Availability, Performance & Quality) KPIs
- Aggregate and compute the information and KPIs required for the Andon dashboards from the PLC and MES data sources.
- Perform off-line alarm/fault and OEE analytics.
- Feed real-time asset events and meter readings to the cloud-based CMMS system via a REST API:
- Critical faults automatically generate electronic work orders without operator intervention.
- Asset meter readings (run hours & cycle counts) are automatically sent periodically which trigger PMs
ASSET PERFORMANCE MANAGEMENT SOLUTION
NeoMatrix was awarded the bid due to our technical approach and relevant MES experience. Our solution utilizes the Ignition platform from Inductive Automation and OEE Module from Sepasoft. The Ignition platform met the technical requirements of the project and provided the flexibility to design an architecture that can scale with the rapid growth the company will undergo over the next several years.
From a technical perspective the project required connectivity to several disparate data sources, large volumes of data, and a modern visualization requirement. Out of the box Ignition provided the ability to:

- Connect to required data sources:
- Allen Bradley & Siemens PLCs
- SQL Databases
- REST APIs
- Monitor and log 75000 tags in real-time
- Provide a visualization solution to 100+ clients which supports HTML5-compliant browsers
- Provide a platform for modular design with object-oriented data structures and templates enabling rapid configuration and deployment
The asset performance management solution required an architecture that easily scales to both local expansion and new sites around the globe. NeoMatrix took advantage of Ignition’s modular platform and designed a ‘Scale-Out’ architecture.
Edge gateways at each shop handle device data and a front-end gateway handles the client applications. The ‘scale-out’ architecture balances the workload across multiple servers while simultaneously reducing the risk of a single point of failure.
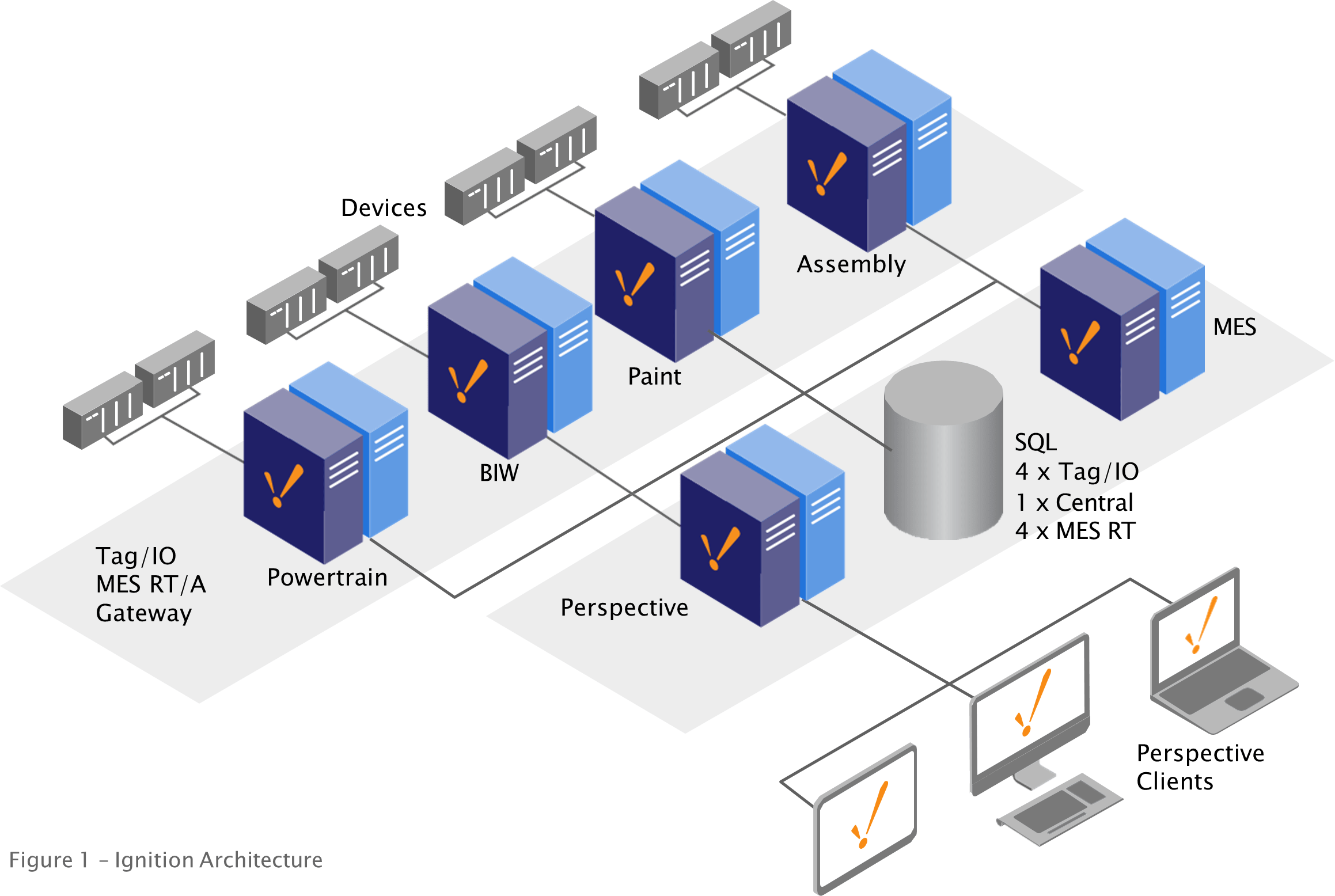